The development of biomass formation technology II
3.Research of biomass densification equipment and corollary equipment
3.1.Research of biomass densification equipmentAt present, our country has three types of densification equipment, they are screw type, piston stamping type and roller die compressing type. The ring die pellet mill is the most popular type of machine, and it can be classified into pellet mill and briquette machine.
The ring die pellet mill can be used to produce fuel and feed pellets, it is well known for its large capacity for pellet production. This kind of pellet mill is featured as large capacity, excellent forming shape, high density and high energy consumption. Nearly all forestry and agro-waste materials can be made into wood pellets with ring die pellet mill, such as: wood chips, shavings, sawdust, peanut shells, coffee husks, paddy straw, sunflower stalks, cotton stalks, tobacco waste, mustard stalk, jute waste, bamboo dust, tea waste, wheat straw, palm husks, soybeans husk, coir pitch barks/straws, rice husks, etc. The final pellets can be used for industrial boilers and large power plants as well as home heating.
3.2. Research of biomass corollary equipment of biomass densification equipment
Selecting of corollary equipment decides the technology route. Taking example of the above technology route of biomass ring die pellet mill, we analysis of the function of corollary equipment and current technology research situation of the process of crushing, drying, removing impurities, mixing of material and cooling.
3.2.1. Crushing equipment
Crushing means the process to squeeze, hit, grind, and saw cutting or other method to destroy the intermolecular cohesive force, achieving the aim of crushing the material to a certain scope of particle size.
The crushing equipment is an insurance of the parameter of particle size of biomass densification. Aiming at different material, it should adopt different kinds of crushing method to improve the crushing efficiency and quality. The main equipment for hitting is hammer type crushing machine to hit the feedstock by hammer. This kind of equipment usually has big size, and the contact surface of feedstock and hammer is much larger which are fit for biomass material with less moisture content and low tenacity, like bean stalk, cotton stalk, sunflower stalk etc. The equipment for saw cutting is the chopper which can process biomass material with high tenacity and high moisture content, like rice, wheat and cotton etc.

3.2.2. Drying equipment
The aim of drying process is to ensure the proper moisture content of raw material for densification, and it can be classified into natural drying and artificial drying. The natural drying means to dry the material by means of solar energy and natural wind. The artificial drying means to dry the material by means of high air current which heated by liquid or coal gas in very short period of time. The natural circumstance has big influence to the moisture content of biomass material, and it can not adapt to the demand of industrialized production. In order to get the proper moisture content for densification, the artificial drying method must be adopted to meet the demand of moisture content for densification through drying. This way of drying is not being affected by the climate, but it has big requirement to the equipment with big investment.
The common type of drying machine are classified into atomizing drying machine, fluid-bed drying machine, air current drying machine, rotary drying machine and conduction drying machine. It is necessary to chose proper equipment for drying. On the basis of the character of biomass material and the drying condition, we usually chose the air current drying machine and rotary drying machine. Drying process is an operation unit with big energy consumption, and the temperature for drying of biomass material is usually between 40-70℃, adapting to the technology of solar energy of low temperature application, to fully utilize the technology of solar energy, saving the traditional energy, decreasing the energy consumption of drying equipment.
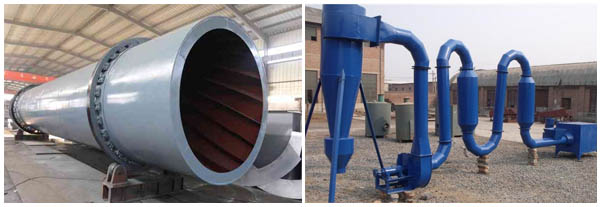
3.2.3 Equipment for removing the impurities
Our country has rich resource for biomass energy, most of the resource comes from direct purchasing from the farmers, mental scrape, stones and dust as well as the thread of cord and other impurities are the primary impurities. The metal scrape, stones and dust increase the wearing of the key equipment of the production line. Thread of cord and other impurities may block the material for conveying, to affect the uniformity and stabilities of conveying of feedstock.
For the metal scrape, the magnet should be used to remove them; the thread of cord and other things can be removed through the design of auger device to make them twin on them and remove regularly; the stones can be removed through the air separation equipment and vibration sifter according to the physical characteristics of the stones and stalks. The finished product of pelletizing technology usually has three type of specification with the diameter of 6mm, 8mm and 10mm. while for the briquetting densification product, and the diameter is not less than 25mm. The pelletizing has high standard towards the impurities content, especially for the impurities of sandstones, it has much strict standard.
For the impurities of iron content, the flat type de-ironing separator, Magnetic grating de-ironing separator and RCQ can be selected to use on account of the influence of the features of feedstock. For the sandstones, the vibration sifter or the shuttle board etc can be used on the basis of the frictional characteristic of the feedstock. Also, the pneumatic concentration should be adopted according to the density of material. Application of technology innovation removes the impurities of feedstock, to design different technology route on the basis of the features of impurities.
3.2.4 Feedstock mixing equipment
One important parameter during the process of densification of biomass solid is moisture content of raw material, the proper moisture content of biomass plant not only transmit the pressure of roller, but also act as lubrication to promote the formation of raw material. In our country, the biomass material is complicated. After researching, we make a conclusion that the proper mixing with other material is advantageous to the formation of biomass for the aim of changing the main material’s features and formation capacity. At the same time, the moisture content of the formation material can be changed through the way of mixing with other feedstock, to save the frying process and save the traditional energy. In addition, the feedstock whose moisture content is lower than the standard for densification should add proper moisture content to humidifying them in order to ensure the universality of material for formation. Mixing of biomass material ask for the uniformity of mixing of material and the appropriateness of adjustment of moisture content, as well as the species of raw material, portion of mixing of material and the influence of the thermal value.
1) the research of difference of each of the feedstock’s feature and the mixing material’s feature decided the basis of researching of the ingredients of mixed material. This kind of mixed feature is the linear superposition of each feedstock features or the nonlinear combination, its principle of features require testing and theory researching to establish the corresponding treatment mode. During the researching of biomass densification, the research of features of mixing feedstock, the research of principle of feedstock’s portion effect to densification, as well as the influence of mixing feedstock to the thermal value and clinkering property of finished production is our research direction.
2). Researching the equipment of feedstock mixing
Research of mechanism of mixing is the basis for the improvement of equipment within the theory research and all the other jobs. Key to design of mixing equipment is to ensure the uniformity of mixing of feedstock, considering the residue of mixing on the basis of shortening the mixing time, wearing and energy consumption of equipment etc. To control the mixing equipment, the working condition, parameter volume controlling and difficulty, operational convenient etc should be considered.
3.2.5 Densification equipment
The biomass compression and mold equipment takes crop straw which mainly are corn stalk, tree branch, pasture, sawdust, wood shaving and other stalk biomass material as raw material , it is an professional equipment to compress the material into briquette. The mainly biomass formation equipment are biomass pellet mill and biomass briquette machine. Biomass briquette machine also called straw briquette machine when compressing the stalk crops. For the briquetting of stalk, the first step is to cut the material with length of 20-50mm and proper moisture content by hay cutter or rubbing machine. Then the material is transport through the feeding machine and enters into the briquetting machine for processing as briquette. The density of briquette is about 0.6-1.0 g/cm3, which is easy to transport and storage. The processed stalk has overcome the difficulties of stalk’s own features of light weight, big volume, easy to be affected by the outside condition of wind, snow and fire, to meet the demand for commercialization. The corn stalk, bean stalk is usually compressed as feed which are called the hard bread of ruminants. The stalk can also be compressed as fuel which broadens the resource for briquetting. It is necessary to pay attention to that the material can not be enzymatic. For the windy area, it is necessary to remove the dust. The moisture content of the briquette should be lower than 15%. For the compression of biomass fuel, it is comparatively simple without thinking of the issues of enzymatic and dust elimination.

In order to overcome the disadvantages of complexity and high consumption of biomass pellet fuel formation equipment, in recent years, the exploring research has been carried out in the aspect of biomass densification technology at home and broad. The densification processing often use the way of screw—die hole compressing formation or roller---ring die hole compression, or roll ring die compression formation. This kind of technology requires much equipment with complicated system, high consumption and high energy cost. Other kind of technological school is to put high pressure to the die chamber which makes the biomass material in the chamber undertake pressure to densification. It is usually use hydraulic pressure as the driving force to push the piston which put pressure to the mold, compressing into briquette or stock as fuel. The pressure is up to 100Mpa, it has high consumption, heavy wearing of mold, low efficiency, and the consumption speed ratio is lower than the pellet.
3.2.6 Cooling equipment
During the industrialized production of pellet, the pellet which just compressed from the pellet mill is about 85℃ with about 16% moisture content. Under this condition, the pellet is easy to crush which are easy to enzyme modification during the storage. It is necessary to low the temperature and moisture content through cooling process. The principle of the cooling equipment is to remove the moisture content and decrease the temperature through the cold wind equipment to the hot pellet. The cooling equipment is common to use counter flow cooling machine.
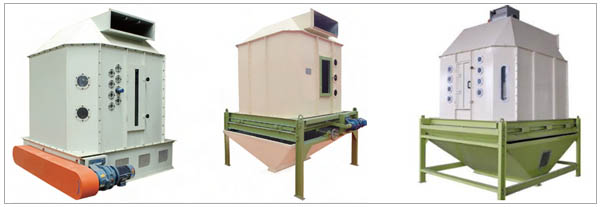
The cooling equipment should meet the demand of ensuring cooling and drying at the same time with reasonable design of volume and proper fan machine. In the design of processing, it should avoid of burst of waist due to the sudden cooling to the pellet, ensuring the enough time of remained in the cooling device, to fully cool and dry the formation fuel under the room temperature less than 5℃. This is based on the condition of feed pellet industrialized production, its temperature is about 100 and the moisture content is below 10% for the biomass compressing formation pellet. Since the product is different, the cooling parameter is changed followed.
4 Existing problems
At present, there are several main problems for the biomass solid formation fuel production line:1) Many technologies have no process of removing impurity or have simple technology of removing, especially for the sandstones with low removing rate, which affect the service life of the key parts, to increase the failure rate of formation production line.
2) The portion of mixing of material depends on the worker’s experience or depends on the storage feedstock amount to mixing them. There are no scientific technological measures to mix and add accessories and there are no research on the mixing effect to the features of quality and texture.
Through continuous conduct propaganda in the market and government supply in recent years, there are big demanding amount in the biomass formation conference in 2015. Now, reserve of conventional energy like oil, gas and coal etc is decreasing with high price, which increase the investment input for the large scale generation, most of the plants has converse to use biomass pellet. Now the consumption of biomass energy has account for 14%, listing the No.4. The portion is still rising, and the market demand will be much more in 2015.
Although there are still problems existing in biomass solid formation fuel production line, we believe that with the development of biomass forming technology and reformation and innovation of pellet mill, we would conquer these problems and improve the quality and utilization of biomass pellet fuels. As one of the leading pellet mill manufacturers in China, KMEC would like to do our part for the development of biomass formation technology, continually improve the quality of our pellet mill and engaged in high-tech products.
The development of biomass formation technology I
--------------------------------------------------------------------------------------------------------------------------------------------------
In 2015, the import trend of wood pellet plant is still centered in Europe and Untied States. Europe is importing the pellets in ever higher volumes, burning them for electricity to meet renewable energy targets. The demand has transformed the U.S. Industry, promoting a doubling of biomass exports last year.
News
- Small Pellet Machine Manufacturer-Kingman
- Application of Wood Pellets and Use of Biomass Pellets
- From Fossil Fuel into Biomass Pellet Fuel
- Biomass Pellet Making Machines Market
- Applying of pellet stoves for home use
- Highland pellets to build $130 million facility in arkansas
- How to deal with the blocked hammer mill
- How to Make Wood Pellets with Sawdust
- The government policy promotes the development of biomass fuel
- Market analysis of biomass pellet fuel
- Strategic positioning of renewable energy
- Biomass energy has pass through the pre assessment
- The key point of deep processing of biomass pellet
- Harbin is promoting the development of biomass machinery
- The development of biomass formation technology I
- The development of biomass formation technology II
- Biomass energy industry is now going full tilt in 2015
- Rapid increasing demand of sawdust pellet on the market
- Pellet fuel market in EU
- Chinese Biomass Energy Conference held in Beijing
- Future market development of straw pellet mill
- Peanut Shell Pellet Mill Makes High Quality Pellets
- The utilization of straw is only 5%, biomass energy needs our attention!
- Corn straw pellet machine relieves the tight supply of fuel energy
- Reasons for loose or not forming of biomass pellet mill